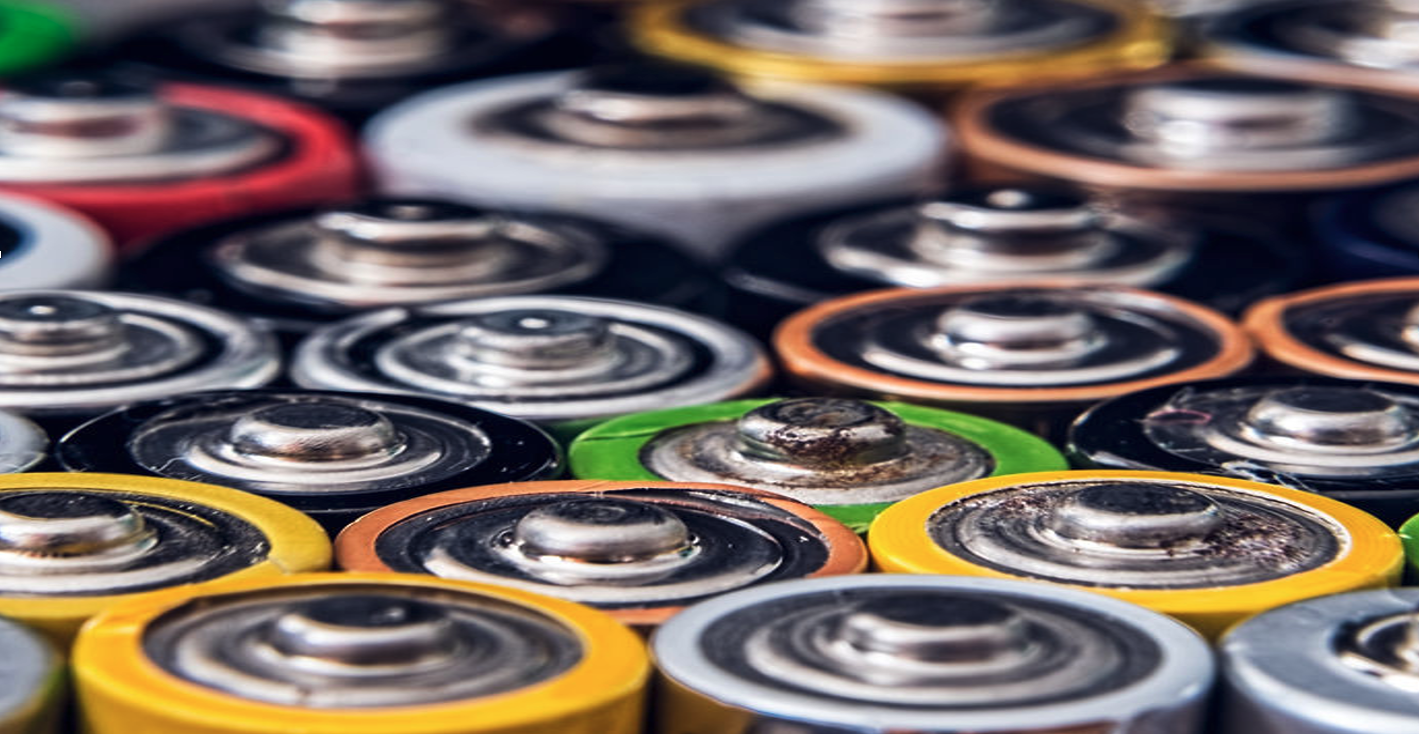
Why we invested in Metastable
April 3rd, 2023 – The global lithium-ion battery recycling market is valued at US $2.54 billion and with a CAGR of 38%, and it is expected to reach $24.93 billion by 2028. In India, with small reserves of lithium available, there is an increased reliance on lithium-ion cells imported from markets such as Taiwan and China. On an annual basis, India generates approximately 50,000 tonnes of lithium-ion battery waste and only 10% of the total battery solid waste in India forms part of the formal recycling value chain, while the balance is often either incinerated, not safely disposed of or accumulates in landfills.
The Rise of Electric Vehicles (EVs) and Importance of Battery Materials
According to the International Energy Agency, nearly 10% of global car sales were electric in 2021, four times the market share in 2019. This brought the total number of electric cars globally to approximately 16.5 million, triple the amount in 2018. Global sales of electric cars have kept rising strongly in 2022, with 2 million sold in the first quarter, up 75% from the same period in 2021.
In the case of India, by 2030 approximately 40-45% of all two-wheelers (2W) and 15-20% of all four-wheelers (passenger vehicles) sold in India will be electric. This has now prompted a large demand for rare earth metals, to manufacture lithium-ion batteries for these EVs. As the EV industry grows and matures, battery recycling and reuse will become vital for both supply chain and circular, low-carbon responsibility. The boom in EVs could leave India with as much as 145,000 tons of used lithium-ion batteries in need of recycling by 2030[1]. Recycling will bring down the costs of batteries and lead to a pathway where by 2030, India could account for about a third of the global demand for EV batteries. Using recycled battery materials as inputs for new battery manufacturing would ease demand pressures on major commodities and reduce batteries’ resource footprints.
Moreover, beyond the electric vehicle use, case, battery energy storage can enable the transition to a sustainable and secure energy system based on renewable sources, with reduced greenhouse gas emissions and enhanced available energy. There is a growing demand for batteries in stationary clean energy grid storage applications which replace diesel generators, given India’s commitment to building renewable energy installation such as solar, hydro, wind and bio-power.
Regulatory Mandates around Recycling
Globally, governments have instituted policy frameworks, bills and mandates around the promotion of recycling technologies which can recover up to 95% of battery materials. The objectives are to become cost-efficient, reduce dependence on import suppliers and encourage battery longevity, but also to dispose of waste materials in a responsible, low toxic manner, to reduce further carbon emissions into the atmosphere.
In the United States, the Department of Energy is working to allocate $335 million in funding for lithium-ion battery recycling included in President Biden’s Bipartisan Infrastructure Law instituted in November 2021. This is in addition to approximately $60 million in funding for second-life applications and recycling processes for EV batteries.
In the EU, the requirement is that least, 50% of a battery’s weight must be recycled, and from 2025, this requirement will increase to 65% for lithium-ion batteries and to 70% from 2030. Another provision in currently proposed EU regulations is the concept of ‘battery passports’ which help to inform consumers on contents, materials origin, and the battery’s environmental impact (traceability).
In India, the Government of India (GoI) brought batteries under the Extended Producer Responsibility (EPR) mandate under the revised Battery Management Rules in August 2022, which dictated that all waste batteries should be collected and sent for recycling or refurbishment, and it prohibited the disposal or incineration of this waste in landfills. Prescribing the use of a certain amount of recycled materials in the making of new batteries, as well as the minimum percentage of materials recovery from waste batteries will:
Reduce the dependency on new raw materials
Promote investment into recycling technologies
Contribute to a cleaner urban ecosystem
Metals such as nickel are utilized in other applications such as corrosion-resistant plating iron and brass, coating chemistry equipment, and manufacturing certain alloys that retain a high silvery polish. Cobalt is also used in many alloys (superalloys for parts in gas turbine aircraft engines, speed steels, cemented carbides), in magnets and magnetic recording media, as a catalyst for the petroleum and chemical industries, and as drying agents for paints and inks. This proves that there is a growing demand from other industries (battery, steel, aircrafts, paints and others) for rare earth metals.
The Need for a Greener Recycling Process
The existing methods of battery recycling and extraction of rare earth metals – pyrometallurgy and hydrometallurgy – are opex-intensive, involve intensive heat and chemicals, are not as cost-efficient, and lead to higher carbon emissions in the process.
With the rising regulations around the carbon accounting and disclosure it is becoming important for the battery manufacturers and producers to maintain sustainable recycling practices. Batteries contain contain corrosive materials and heavy metals such as cobalt, nickel, manganese, iron and phosphorous. If placed in landfills, the toxic materials can leak into the soil and penetrate the water supply, and if incinerated, toxic fumes can decrease the quality of the air. There is therefore a need for recycling processes which use lower carbon, higher salvage value, a cleaner supply chain, lower volumes of water and lower heat in the form of power, to achieve the same metal extraction outputs.
We chose MetaStable Materials because of the following factors:
Unique, patented ‘carbothermal’ recycling process for rare earth materials using a lower use of energy and chemical free components to significantly reduce cost
High environmental impact in providing a lower emission alternative to mining new metals, as well as traditional recycling methods such as pyro and hydrometallurgy
Catering to a large addressable market of EV batteries, with countries focusing their domestic supply chain rather than relying on foreign imports on developing
Commercial and technical-minded founders relevant backgrounds in metallurgical and material science, mechanical engineering and supply chain management
Theia Ventures is proud to join MetaStable Materials’ $2M seed round led by Peak XV (formerly Sequoia India & SEA) with participation from Speciale Invest and other strategic angels, to transform battery recycling using a green and cost-efficient process.